Home » Posts tagged 'concrete services'
Tag Archives: concrete services
Contractors Can Assess Your Concrete Repair Needs and Recommend a Course of Action
The first step in any concrete repair is evaluation of the extent of damage. Then proper preparation can begin.
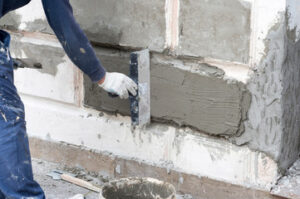
The right equipment and high-quality materials ensure repairs are done correctly and last. Having an experienced contractor is essential. A skilled contractor will also guide preventative maintenance to extend the life of the concrete.
Concrete cracks can be a sign of deeper structural problems. When ignored, they can lead to deterioration and possibly compromise the safety of people using the structure. Fortunately, concrete crack repair is relatively easy and straightforward. There are several different techniques to choose from, but it is important that the correct materials and drying conditions are used to ensure that the crack repairs last. SUNDEK contractors have years of experience in concrete crack repair and can assess the condition and recommend a course of action to restore the strength and longevity of your structure.
The curing process for concrete causes it to shrink, which creates hairline cracks. These are usually not a structural concern, but they can be repaired to prevent water from entering the crack and further deteriorating the concrete or masonry.
One of the most common methods for repairing cracks is routing and sealing. This involves enlarging the crack, filling it with appropriate materials and then sealing the surface of the concrete. This method is suitable for repairing both large and fine pattern cracks. It is also ideal for preventing the cracks from spreading further.
If you are repairing cracks on concrete surfaces that are exposed to heavy loads, then consider adding pre-stressing steel to the structure. This will add a compressive force to the cracks and improve their stability.
Another option for crack repair is using epoxy injections. This technique involves drilling holes into the concrete and then filling them with epoxy. This method is ideal for repairing cracks that are small and active, but it is not a good solution for addressing cracks that have already begun to spread.
When choosing a concrete crack repair material, it is important to consider the dimensional characteristics, freezing and thaw resistance and chemical composition of the product. You should also consider the crack width and whether it is active or dormant. Additionally, it is a good idea to select a product that contains a bonding agent, which will improve the adhesion of the repair material to the concrete substrate. Finally, the temperature range that the material can withstand is also an important consideration.
Expansion Joint Repair
Concrete expansion joints are spaces between separate slabs of concrete that allow for the natural expansion and contraction of concrete without causing damage to the adjacent concrete. They also absorb vibration and seismic stresses.
When the expansion joint becomes damaged or fails, it can cause concrete cracks that may spread to other parts of the concrete structure. This makes concrete expansion joint repair a key component of concrete repairs.
Expansion joints are usually filled with backer rod and sealed with caulk. Backer rod is a soft, pliable filler that partially fills the expansion joint and allows the sealant to extend to the full depth of the joint. It is inserted into the concrete prior to pouring and then sealed. During construction, it is not possible to pour the entire concrete slab in one day so concrete is poured over multiple days. Expansion joints are then left consciously in the building to accommodate for thermal and ground settling changes that may damage the concrete if they are not controlled by expansion joints.
Over time and with heavy traffic, the caulk within the expansion joints can become dislodged, leaving the expansion joint exposed to water infiltration and other damaging environmental elements. The expansion joint needs to be replaced and properly sealed to protect it from the elements.
Expansion joint failure is a serious problem in industrial settings where acidic chemicals and other corrosives can attack the concrete. The result is a slow-building structural weakening process that can cause massive and costly problems later on. The best way to prevent this is by regularly performing concrete expansion joint repair and keeping the joint well maintained.
Using Belzona 2911, condition the internal part of the expansion joint to prepare it for the application of a concrete expansion joint sealant. Using a hand-held sprayer, apply the mixed Belzona 2221 to the full depth of the expansion joint. When the application is complete, remove the tape masking the area.
Taking advantage of our professional concrete expansion joint repair service will protect your concrete from cracking, weed growth and deterioration. Contact us today to request a free onsite consultation and cost estimate.
Repairing Cracks and Voids
When a concrete structure begins to deteriorate, cracking and honeycombing are common problems that must be addressed. In some cases, the deterioration is so severe that concrete replacement becomes necessary. When this occurs, it is vital to use the correct method for repairing the concrete to ensure that the new concrete makes an integral bond with the existing material.
The first step is to identify what is causing the cracking or honeycombing. This will require a thorough inspection of the concrete structure. The inspection should include looking at the structure as a whole, taking into consideration all factors that could have contributed to the problem.
A good option for smaller cracks in concrete is to use a concrete crack repair product such as a latex or polyurethane crack filler. These products are ideal for repairing cracks that are not structurally significant or active, and they can be easily sealed to prevent water ingress. However, it is important to note that these types of products do not strengthen the concrete and are therefore only a short-term solution.
For larger cracks in concrete, there are a number of different concrete repair techniques available. These include epoxy injection, routing and sealing, grouting, stitching, drilling and plugging, and gravity filling.
Epoxy injection is a great concrete crack repair solution for wider cracks and is often used to stop leaks in wet or leaking concrete structures. This technique is also used to treat a wide range of chemical and environmental damage. The injection process involves inserting a polyurethane resin into the crack, which reacts with the water present to form a waterproof seal. This is an effective method for repairing non-dormant cracks as well as active cracks in concrete.
Other crack repair methods are more advanced and involve placing a layer of concrete directly over the existing concrete. This is a more permanent solution, but it requires careful consideration of the conditions and design of the concrete structure. It is critical that the new concrete is poured with a low water-to-cement ratio to minimize differential shrinkage cracking and that a high percentage of coarse aggregate is used to maximize strength.
Repairing Structural Defects
While cracks and honeycombing are visible to the naked eye, other damage may not be as obvious. It’s critical to inspect concrete structures frequently, and address issues as soon as they appear to avoid escalation and save on costly repairs in the future.
Inspecting concrete damage isn’t just about identifying its presence, but also understanding the cause. Generally, structural defects are caused by either physical or environmental factors. Physical causes include abrasion, erosion and cavitation; environmental factors can include corrosion of reinforcing steel, drying shrinkage, thermal gradients and water penetration.
If it’s determined that the cause of a problem is physical, the structure can be strengthened using various methods, including grouting and injection. Epoxy injection is a full-depth repair technique that works with both active and dormant cracks. This method is highly recommended for repairing concrete that is suffering from fatigue due to heavy loads.
Another way to strengthen a concrete structure is through carbon fiber reinforcement, which helps increase load-bearing capacity by adding a compressive force to the slab. This method can also be used to enhance the appearance of concrete surfaces.
Structural issues that aren’t addressed promptly can lead to deterioration and even structural failure of the entire concrete structure. This can be very expensive to repair and can cause significant downtime and disruptions to operations.
Concrete repair techniques are an essential part of maintaining safe and functional structures. The key to minimizing the need for frequent repairs is addressing problems promptly, as well as ensuring that repairs are made with quality materials and properly executed to guarantee long-lasting results.
When selecting a concrete repair material, it’s important to consider its viscosity and chemistry, as well as the surface it will be bonding with. Ideally, a concrete repair material should be similar in texture and chemical makeup to the existing concrete, as this will provide the best possible strength and durability. Additionally, a repair material should be low in shrinkage to prevent debonding from occurring during the curing process. Lastly, it’s important to consider freeze-thaw resistance and allow for water vapor transmission to avoid damaging the concrete with trapped moisture.
Factors That Affect the Success of Concrete Repair
Concrete repair requires a combination of many factors to be successful. These include physical properties of the repair material, such as drying shrinkage and modulus of elasticity, permeability, and freeze-thaw durability.
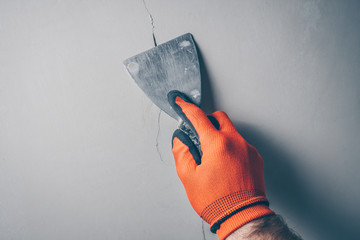
The location of the damage must be evaluated and the correct preparation of the old concrete should be done to ensure a good bond with the new repair. Visit https://www.concreterepaireauclaire.com/services for more details.
Crack repair is an important part of concrete restoration. This is especially true for cracks that are deemed active and non-dormant and that have a significant effect on the structural integrity of a structure or its safety. Identifying what type of cracks are present and the status they are in is critical to selecting suitable crack repair methods. Cracks indicating a design, construction or material failure may be structurally significant and therefore require a different repair method than cracking that is due to intrinsic volume changes such as drying shrinkage or thermal expansion and contraction.
When repairing a crack, it is important to first clean the crack and remove any debris from the surface. This will ensure that the crack repair is adhered to a clean surface and that any potential water ingress from the crack will be sealed. Then, the crack must be routed and sealed with an appropriate filler for that type of crack. Routing and sealing is a simple process that involves widening the crack and filling it with a sealant that can move with the crack. For example, epoxy or polyurethane resins can be used as a concrete crack filler and are ideal for widening and sealing non-dormant and active concrete cracks. They can also be used for wet cracks when combined with a moisture tolerant epoxy.
An alternative to a poured epoxy crack filler is the use of concrete caulks. These can be injected into the cracks to form an effective seal, and they will allow the concrete to flex with its natural movements without breaking down. Moisture tolerant silicone and acrylic caulks can be used for this purpose.
Another option is to inject a wet crack with a hydrophilic polyurethane resin. This will be able to react with the water within the crack and chase it, effectively closing the leakage. This is a good choice for wet cracks that cannot be dried out using moisture tolerant epoxies. This injection technique can be used for both dormant and active cracks, but it is important to anticipate future movement and cater for this with the design of the structure.
Filling Cracks
Concrete is strong in compression, but weak in tension, which results in cracking during the curing process. These cracks are mainly due to exothermic chemical reactions, thermal expansion or contraction and drying shrinkage. They are not structurally significant and may not even affect the load-carrying capacity of the concrete. Cracks that imply a design, detailing or construction error, however, raise serious concerns and may be detrimental to the performance of the concrete structure.
It is important to identify and rectify the causes of the cracking before attempting any repairs. If the cracking is due to the lack of a suitable aggregate or if a concrete mix was incorrectly designed or poured, the cause must be addressed to prevent it from occurring again.
Once the cause has been identified, a repair procedure should be selected that is appropriate for the type and size of crack. Small cracks can be filled with a commercial masonry concrete crack filler that is sold in cartridges to fit a caulking gun or a vinyl concrete patching compound that can be applied with a wet margin trowel and smoothed with a putty knife. It is important that the crack area be thoroughly cleaned of any loose debris to ensure a good bond. It is also advisable to dampen the area to avoid pulling moisture from the fresh concrete repair material, as this will decrease its adhesion and durability.
In many cases, hydraulic cement is used to repair cracks in concrete. While this product is relatively inexpensive and easy to use, it does not form a good bond with the existing concrete, which can result in the cracks widening over time. For this reason, a stronger repair method such as epoxy injection should be considered for larger cracks.
When using either a commercial crack filler or an epoxy injection system, the concrete should be thoroughly dampened to reduce the possibility of the new material pulling moisture from the existing concrete. In addition, if the crack is going to be exposed to water, it should be covered with a wet burlap sheet or plastic and taping down the edges to keep the moisture in place.
Patching Cracks
Many of the same factors that cause cracking also affect the quality of concrete products. It is very important that they are identified and corrected at the appropriate stage of production to prevent recurrence of the problem. It is easy to see when there is a crack in concrete; however, it takes more in-depth evaluation to determine the cause and severity of deterioration and/or failure.
For minor defects, routing and sealing is a quick and relatively inexpensive repair method. Routing involves sawing or chipping out the affected area, followed by the filling of a chemical grout or epoxy resin. This method is useful for cosmetic cracks that do not extend to the steel reinforcement or the surface of the concrete.
When repairing these types of defects, it is critical that the concrete surface be clean and free of loose debris. This will allow the filler or sealant to adhere to the concrete and thereby maintain its effectiveness.
If the concrete is not sufficiently consolidated before patching, it will become displaced in time and the repaired areas may fail. The addition of a water reducer to the concrete mix will help to avoid this. It is also a good idea to use a mix design that contains less water than the original concrete to help minimize shrinkage cracking.
A good rule of thumb is to use the same ingredients for a repair mix as in the original mix if possible, with the exception of a lower water content. Having the concrete accept an integral bond is one of the most critical aspects of a successful repair.
Concrete patch kits and overlays are often used for the repair of trip hazards, or as a surface cover for spalling concrete. These types of repairs are usually a temporary solution, and can fail quickly as the concrete continues to deteriorate and experience fluctuations in temperature.
Unless the concrete is at an early age, it should be replaced with a fresh batch of replacement concrete to ensure that the cracks will not reappear. Replacement is also a good choice when there are large sections of honeycombing that have not extended to the steel reinforcing bars or to the surface of the concrete.
Repairing Holes
In some cases, concrete repair is needed to address holes caused by corrosion or other reasons. Holes from corrosion are often round with a small opening, while holes from cracks have more of a square-shaped appearance. In either case, these can be repaired using a concrete patching compound or concrete plugs.
It is important to make sure that the existing concrete is a sound, dense material before the application of repair materials. This is critical to ensure that the bond between the existing concrete and the repair is strong enough to withstand the stresses created by thermal expansion and contraction of the repair material. It is also important that the material used for the repair has a compressive strength comparable to the existing concrete.
When repairing a hole, it is important to remove any loose pieces of concrete and to clean the area thoroughly with a wire brush. This is especially important in areas that have been damaged by salt or acidic cleaners. The area should then be swept and rinsed with water from a garden hose.
Once the surface is ready, the hole can be filled with a dry concrete mix. Dry concrete mixes are a popular choice for repairs because of their ease of use and durability. However, it is critical to ensure that the mixture contains no gypsum cement, which can swell when exposed to moisture. It is also critical to follow the mixing instructions carefully.
If the concrete is very deteriorated, it may be necessary to use a concrete replacement method instead of a mortar or dry pack repair. This will involve digging out the old concrete and replacing it with new, ideally tying in any existing reinforcing steel in the process.
Concrete replacement can be a messy process, so it is best done in a garage or other area where the mess can be controlled.
Concrete repair needs to take into account the environment and society, as well as its performance requirements. In order to minimize the impact on the environment, it is critical that the repairs are made quickly and correctly. Increased concrete repair activity due to durability failures contributes to depletion of natural resources, produces massive quantities of waste and inert debris, and causes pollution. Engineers have an essential role to play in designing eco-efficient repair systems that achieve specified levels of durability and strength while minimizing the need for repairs.